How to Create an Effective Quality Containment Plan
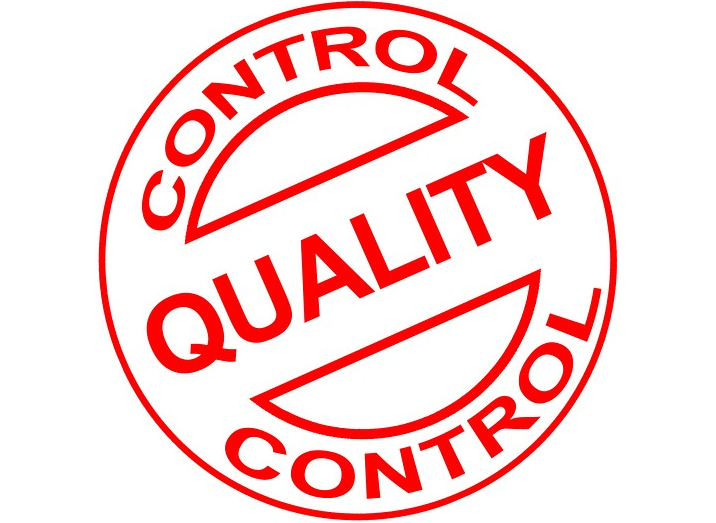
Quality disruption is more common than you may have thought before. They had to recall 2.5 million phones from the market, although they had insisted before that it was safe to use the phone. Although your startup has not reached that level yet, it is always best to think big, especially when it comes to overcoming crises.
A quality containment plan consists of a set of actions to contain nonconformance and prevent it from spilling or escaping your control. Let’s discuss the details below!
Learn the Stages of Quality Disruption
Before we set up the plan, you have to learn the stages of quality disruption:
1. Inspection
An inspection happens during quality control. And if the defective products are identified at this stage, the cost for the recall will be the cheapest.
2. Assembly Line
Some products need to be assembled elsewhere. And there are chances that you miss the nonconformance during the inspection and let those defective parts reach the assembly line. At this stage, the incident may cost you hundreds of dollars.
3. Transportation
When the defective parts are identified during or after shipping, recalling them will be tedious and time-consuming as you will need to coordinate with your shipping partner and ask them to inspect the products for you.
4. Consumers
If your consumer files a report about your defective product, the cost will be the most expensive. You can expect lawsuits and even reimbursement that is worth millions of dollars.
Know Who to Hire
A quality containment project is usually not an in-house task. You hire a service for the job. However, the challenge here is to find the right company that can keep their words. This kind of portfolio should be your standard if you were to hire another containment service provider.
Moreover, ask for the workflow from the provider. For instance, the most conventional one is: suspect identification, holding, locating/inspecting, informing customers, releasing, and dispositioning. Be inquisitive about the workflow so that you can evaluate both the efficiency and hospitality of the provider.
Estimate the True Cost
A containment project will cost you per hour. The longer it is to work on it, the more money you have to spend on it. Therefore, it is way better to hire a provider with a high per hour rate, but they can complete the project fast, than to hire a service with a 20% lower cost but also with a longer time.
Besides, unskilled and untrained inspectors, even though they are cheap, may not do the job appropriately. Your quality disruption is at risk of advancing stages as the containment procedure is on progress.